Atlas Copco air compressor Oil Separator
Why is it necessary to separate oil and water?
The removal of oil from water is a crucial task. Many are likely familiar with the demonstration where a small drop of oil rapidly spreads across a large surface of water. Just one litre of motor oil can pollute up to one million litres of groundwater.
When an oil slick spreads over water, it can block oxygen from reaching the plants and animals below. Oil can also harm wildlife by affecting the insulation of fur-covered animals and reducing the water-repellent properties of birds' feathers.
Another important reason for separating oil from condensate is legal. In many regions, stricter environmental regulations are being implemented, which ban the disposal of water containing oil. Breaching these regulations can result in heavy fines.
The good news is that separators can remove nearly 99.5% of the oil present in compressed air water vapour. Let’s now explore how an oil-water separator functions.
While oil-water separator brands and models can vary, the majority use multi-stage filtration and rely on the principle of adsorption. Adsorption occurs when oil adheres to a surface, driven by its lower density compared to water.
In condensate treatment, separators typically utilize two or three stages of filtration, each using different types of filtration media. Let’s break down each stage to gain a clearer understanding of how the condensate from a compressor is processed.
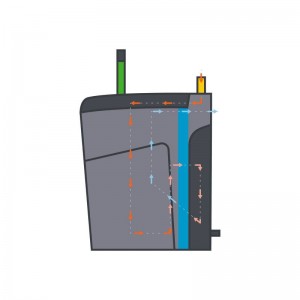
Filtration stages
The condensate, which contains oil, flows under pressure from the compressor into the separator. It first passes through a primary filter, often a pre-filter. To prevent turbulence and reduce pressure, a pressure relief vent is commonly used. This setup enables the gravitational separation of free oils.
First stage
First-stage filters are commonly made from polypropylene fibres, which are designed to attract and hold onto oil, but not water. As a result, oil droplets adhere to the surface of the fibres. These fibres are referred to as "oleophilic" because of their oil-attracting properties. Initially, this filtration media floats on top of the water, but as it accumulates more oil, it becomes heavier and gradually sinks towards the bottom as it nears the end of its useful life.
The second and third stages of filtration
Once the condensate passes through the first-stage filter, it moves on to the main filters, which typically include second-stage and, in some cases, third-stage filters. These stages often use activated carbon (or organoclay for more challenging emulsions) to further purify and "polish" the condensate. Depending on the size and design of the separator, the condensate undergoes one or two additional filtration stages using activated carbon or organoclay.
Last step
By the end of the process, any remaining oil residues in the condensate are gathered. At an ambient temperature of 20°C, the condensate contains 1-2 g/m³ of oil after the first stage, but only about 2-3 mg/m³ of oil remains after separation.
The water left behind is clean enough to be safely released into the sewer system. The oil-water separator has completed its task. In the end, everyone benefits: the company complies with regulations, avoiding penalties while contributing to environmental protection.
How Often Should You Empty an Oil Separator?
An oil separator is critical to the operation of an air compressor, particularly in oil-injected models like those produced by Atlas Copco. This essential component separates oil from the compressed air before it leaves the compressor, ensuring that the air output remains clean and free from contamination that could affect downstream equipment or processes.
The Importance of the Oil Separator
In oil-injected air compressors, oil is used to lubricate and cool the compressor’s moving parts. During the compression process, some of this oil can mix with the compressed air, which is where the oil separator comes into play. Its job is to efficiently separate this oil from the air, returning it to the compressor system and ensuring that only clean, dry air is delivered to your applications.
Over time, as the air compressor operates, the oil separator will collect more oil and water, which needs to be drained regularly to maintain the performance and efficiency of your compressor system.
How Often Should You Empty the Oil Separator?
The frequency of emptying the oil separator can depend on various factors, such as the size of the air compressor, the operating environment, and the specific requirements of the equipment. However, as a general rule, oil separators should be emptied at least once every 500 to 1,000 operating hours.
- Operating Conditions: If your compressor operates in a dusty or humid environment, or if it’s under heavy usage, you may need to empty the oil separator more frequently. Regular checks during maintenance will ensure that the oil separator isn’t becoming too full, which could lead to reduced efficiency and potential issues with air quality.
- Manufacturer’s Recommendations: It’s important to follow the specific guidance provided by the manufacturer for your model of air compressor. For Atlas Copco models, you should refer to the maintenance schedule and guidelines in the user manual, which will give you more precise intervals based on your compressor's model and usage patterns.
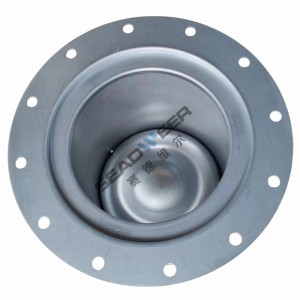
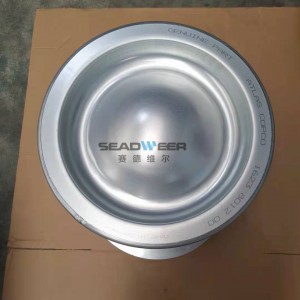
1092063102: A Key Atlas Copco Oil Separator Part
If you work with Atlas Copco compressors, the oil separator is an essential component to maintain. A commonly referenced part is 1092063102, a replacement oil separator element designed for Atlas Copco air compressors. This part ensures that oil is efficiently separated from the air to keep the system running smoothly and efficiently.
Why Regular Maintenance is Crucial
Regular maintenance, including draining the oil separator and replacing worn parts like the 1092063102 oil separator element, is crucial for extending the lifespan of your Atlas Copco air compressor and maintaining its optimal performance. Neglecting this maintenance can lead to oil contamination in the compressed air, which could damage sensitive downstream equipment, leading to costly repairs and downtime.
A Complete Service Solution with 20 Years of Expertise
As a professional exporter of Atlas Copco products in China, we have over 20 years of experience in providing complete solutions for industrial air systems. Our team of experts not only offers the supply of genuine Atlas Copco parts, including the 1092063102 oil separator, but also provides comprehensive maintenance and repair services. Whether you need regular service or urgent repairs, our experienced technicians are ready to ensure that your equipment runs smoothly, efficiently, and with minimal downtime.
We offer a one-stop solution, providing everything from parts and installation to maintenance and troubleshooting. Our professional maintenance team ensures your equipment is well taken care of, reducing the likelihood of costly disruptions.
Maintaining an Atlas Copco air compressor involves regular maintenance of key components like the oil separator, ensuring that the compressor operates effectively and continues to deliver clean, dry air. By following recommended maintenance schedules and replacing parts like the 1092063102 oil separator element as needed, you can extend the life of your equipment and avoid unnecessary downtime.
With our 20 years of experience in providing professional Atlas Copco solutions, we are your trusted partner for parts, service, and support. Contact us today for a complete service package and ensure your air compressor remains in top condition.
2914011500 | HOUSING | 2914-0115-00 |
2914010700 | BUSH | 2914-0107-00 |
2914010600 | O-RING | 2914-0106-00 |
2914010500 | GASKET | 2914-0105-00 |
2914010400 | RING | 2914-0104-00 |
2914010300 | STUD | 2914-0103-00 |
2914010200 | NUT | 2914-0102-00 |
2914010100 | WASHER | 2914-0101-00 |
2914010000 | STUD | 2914-0100-00 |
2914009900 | ROD | 2914-0099-00 |
2914009800 | HOUSING | 2914-0098-00 |
2914009200 | BUSHING | 2914-0092-00 |
2914009100 | BEARING | 2914-0091-00 |
2914009000 | HUB-DRUM | 2914-0090-00 |
2914008900 | SPRING | 2914-0089-00 |
2914008600 | PIN-SPLIT | 2914-0086-00 |
2914008500 | NUT | 2914-0085-00 |
2914008400 | SEAL | 2914-0084-00 |
2914008300 | RING | 2914-0083-00 |
2914001600 | BRAKE-DRUM | 2914-0016-00 |
2914001400 | TIGHTENER | 2914-0014-00 |
2914000900 | TORSION BAR | 2914-0009-00 |
2914000800 | O-RING | 2914-0008-00 |
2914000700 | BUSH | 2914-0007-00 |
2913307200 | FILTER OIL | 2913-3072-00 |
2913160600 | FUEL SUPPLY PUMP | 2913-1606-00 |
2913124500 | GASKET | 2913-1245-00 |
2913123000 | GASKET | 2913-1230-00 |
2913105300 | NARROW V-BELT | 2913-1053-00 |
2913105000 | NARROW V-BELT | 2913-1050-00 |
2913002900 | PH METER | 2913-0029-00 |
2913002800 | REFRACTOMETER | 2913-0028-00 |
2913002400 | SEAL MOUNTING TOOL | 2913-0024-00 |
2913002300 | LIP SEAL SLIDING BUS | 2913-0023-00 |
2913002200 | BELT TENSIONING TOOL | 2913-0022-00 |
2913001900 | KIT | 2913-0019-00 |
2913001800 | PC CARD DDECIV | 2913-0018-00 |
2913001700 | MPC CARTRIDGE | 2913-0017-00 |
2913001600 | DDECIV READER | 2913-0016-00 |
2913001200 | TOOL | 2913-0012-00 |
2913001000 | TOOL | 2913-0010-00 |
2913000800 | TOOL | 2913-0008-00 |
2913000700 | TOOL | 2913-0007-00 |
2913000600 | TOOL | 2913-0006-00 |
2912639300 | SERVICE KIT OILTRONI | 2912-6393-00 |
2912638306 | SERVICE PAK 1000 H Q | 2912-6383-06 |
2912638205 | SERVICE PAK 500 H QA | 2912-6382-05 |
2912637605 | KIT | 2912-6376-05 |
2912637504 | KIT | 2912-6375-04 |
2912627205 | SERVICE PAK 1000H QA | 2912-6272-05 |
Post time: Feb-11-2025